Where Can Laser Welding Be Used?
Automotive
Welding of numerous parts such as air bag initiators, batteries and fuel injectors for high strength welds.
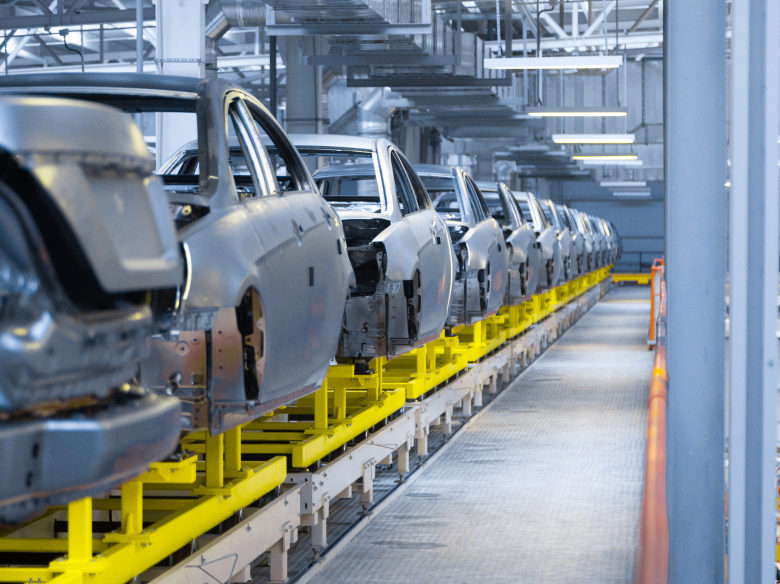
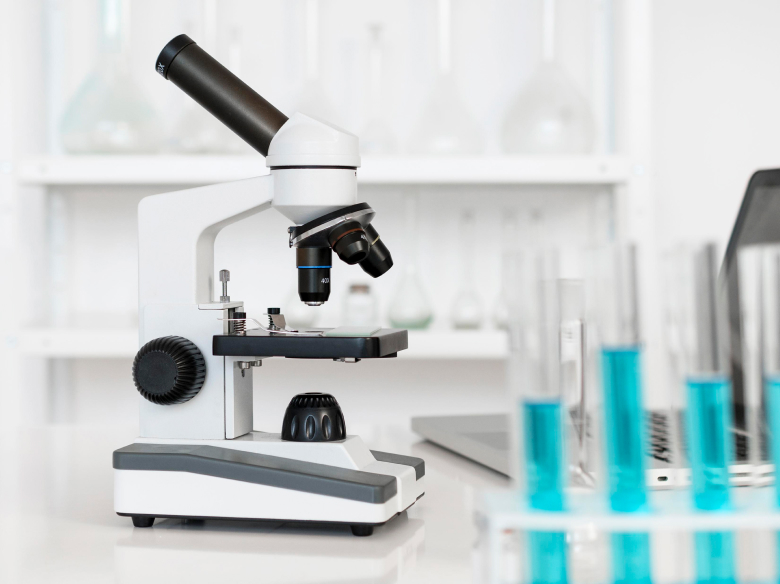
Medical
High integrity, hermetic seals and welds of many precise pieces of innovative medical equipment for ultimate precision.
Aerospace
Welding of different varieties of metals is critically important in this industry while laser welding guarantees precision, no damage for the materials due to precise heat input to desired area and high strength welds.

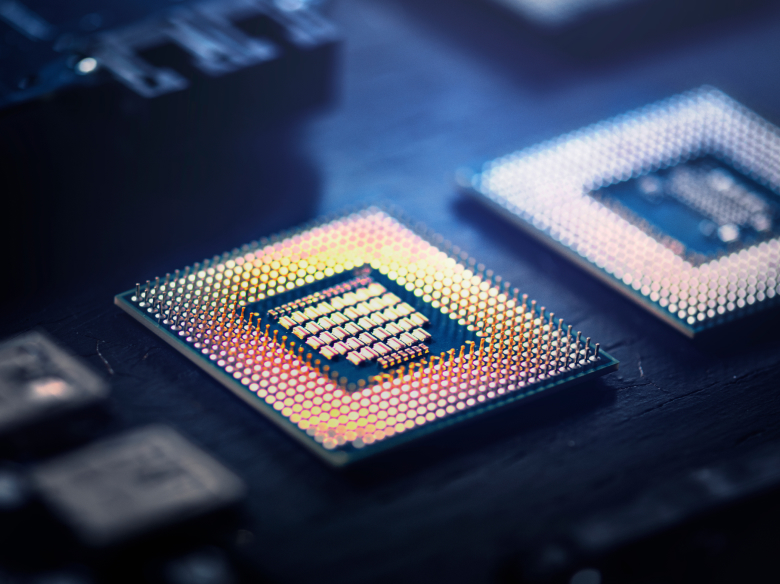
Semi-conductors
Small welds are created in micro sized semiconductor parts because of laser welding precision and possibility to create complicated joints.
Electronics
Welding is used in the production of various electronic components of equipment such as LED’s, mobile phones, TVs, etc. to create precise and complicated joints.
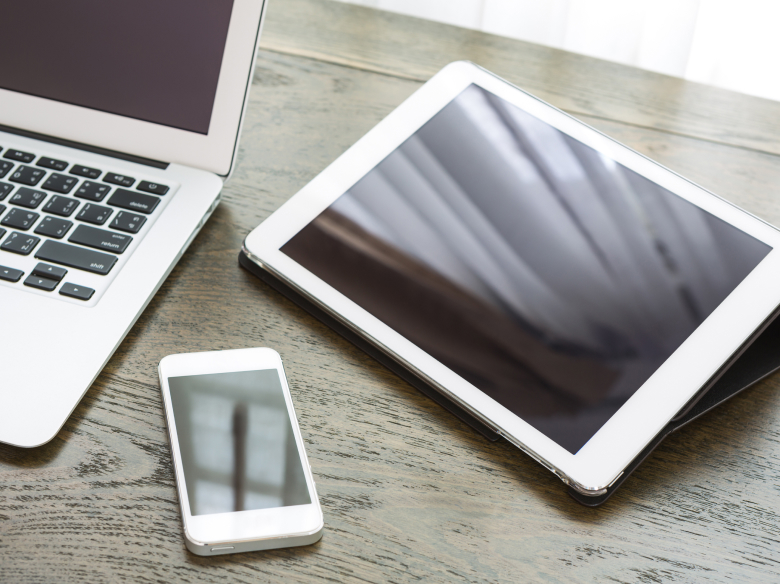
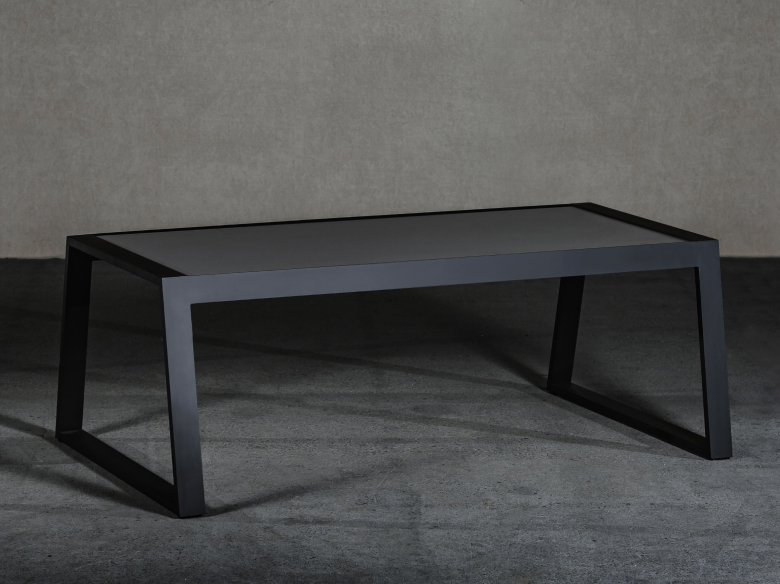
Furniture Manufacturing
Precise aluminum and steel components welding with laser possibility to keep a memory of desired parameters for next welding to achieve consistent results and save up a lot of preparation time.
Materials
A whole range of materials can be worked with in this process:
- Stainless-Steel
- Copper
- Aluminium
- Gold
- Silver
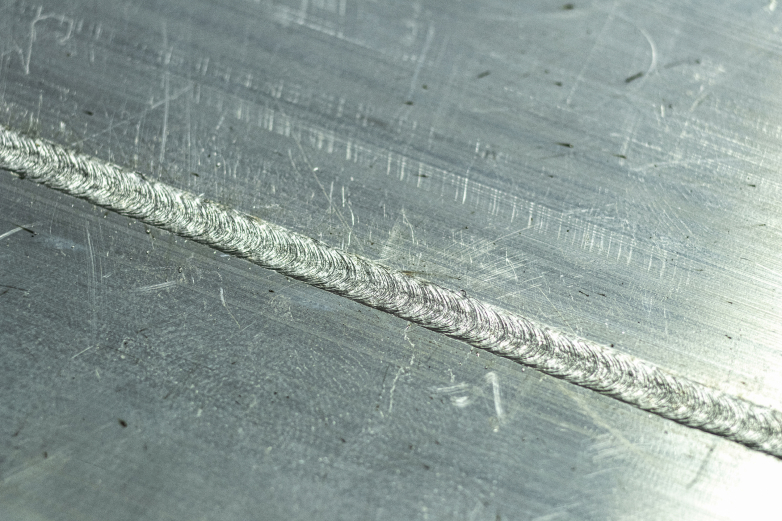
Advantages
- Close to zero physical distortion when thin large sheets are joined, laser welding avoids thermal and physical distortion of the end product without additional processing.
- Low welding oxidation Fiber laser welding method provides ultimately precise heat input to desired area with narrow full penetration weld which makes an aesthetic final result.
- Excellent mechanical properties
laser welding does not affect material or its structural properties. - Easy to operate even for weld beginners due to laser welding memory of set up parameters.
- Very high efficiency laser welding is >5 times faster than MIG and >10 times faster to TIG.
- Long and wide sheets welding
- Cost efficient welding solution low energy consumption.
- Allows welding of sheets with different steel grades and dimensions.
Drawbacks
- Relatively high single-time investment costs compared to traditional methods.
- Fiber laser welding requires a tight fit between the parts to be joined. In many cases it is best to redesign the joint locations to present overlapping surfaces.
- Limited material thickness (today’s maximum 10mm single sided).